Bale Stacker
system saves labor
BY
TOM J. BECHMEN
Once upon a time a farmer could make a few phone calls to
some high school-aged boys, and in short order have a full
hay crew. For a variety of reasons, those days ended long
ago across most of the Midwest.
Facing a labor shortage, many turned to big round bales. Others
bought bale wagons. Kenneth Flock and his son, Mike, Ramsey,
Ind., have found that a different system fits best for handling
most of their hay. They purchased a hay accumulator and bale
fork for grouping, loading, and unloading small, square bales.
Difficulty finding help was one of the key reasons that helped
the Flock's decide to mechanize their hay handling system.
The Flocks have a 50-cow dairy and also operate a fairly large
crop operation.
"We wanted to stay with small, square bales on our better
hay for several reasons," Mike recalls. "If we wanted
to sell hay, we figured we could sell small square bales more
easily.
"Plus, we believed we would have less loss in square
bales (compared to big round bales). And it's easier to feed
the dairy cows and know what they're getting if you're feeding
small, square bales. If you put out a big round bale, you
don't know how many pounds of hay they're getting per day."
Once they were sure they wanted to stay with small, square
bales for their higher quality hay, the choice became which
system to use. Cost was an important factor. To make the accumulator
system work, they needed to purchase an accumulator that trails
behind the hay baler and a bale fork that fits on the tractor
loader. Purchaseing both items was still cheaper than buying
a bale wagon, the Flock's note.
Cost wasn't the only consideration. "We feel this system
is more felxible," Mike says, "If we can get into
a barn with our tractor and loader, then we can get in with
the bale fork to unload. A bale wagon tends to need higher
clearance for unloading. With our bale fork, it's also easy
to load trailers and do other tasks which would be harder
with a bale wagon."
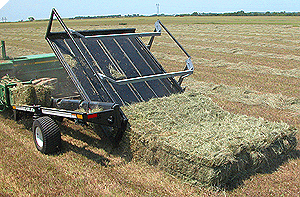
The heart of the system the Flocks use is the bale accumulator.
Manufactured by Hoelscher, Inc., Bushton, Kan., their particular
model of accumulator trails behind the baler and places 10
bales into a group before emptying the hay onto the ground.
When the accumulator cart is full, it trips automatically,
lifts and dumps the bales, and then resets.
Maintaining the same bale length is important when you're
using an accumulator, Ken notes. If he moves into an area
where the windrows are lighter, it's sometimes necessary to
make adjustments to the size of the bale stays as constant
as possible.
Using
the bale fork mounted on the tractor loader, Mike can pick
up the entire 10-bale group and load it on the wagon. On average,
they stack wagons five- or six-layers high. Loading can be
a one-man job, Mike notes. If a second man is available, he
sometimes helps guide the driver and helps position bales.
"About the only secret you need to know is parking the
wagon on a level spot before you begin to load it," Mike
says. Usually, it's possible to retrieve and load 160 bales
in about one-half hour.
|